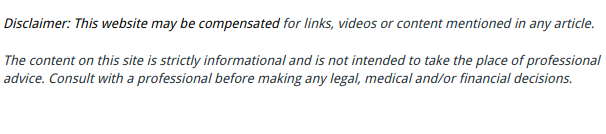

The maker of Charles Babbages Difference Engine, Joseph Clement, was an engineer, industrialist and an early salesperson of taps and dies. Since then, the taps, tap adapters and dies have continued to be critical to industrial production.
During World War II, when the nation was responding to the Allied war needs, the Greenfield, MA tap and die facility was protected with anti aircraft guns. That is indicative of the importance of the machining capabilities of modern industry. Machine tapping, with tap adapters, can be both more accurate and more efficient than hand tapping. Plus, the machine tapping eliminates any possibility of human error.
Machining tools basically do two things with precision, they constrain the workspace and they precisely move the cutting parts. With this ability, precision tools and parts can be made that fall under precise measurements and tolerances. The issues that can occur with both hand tapping and machine tapping are related to the metal on metal cutting that can generate heat. The stock may need to be lubricated with a heat dissipating oil or other lubricant to diminish heat related defects.
Machining is an evolutionary technique, that can be traced back at least to a screw cutting lathe from 1483. It featured direct mechanical control of the pah of the cutting tool. When using some of the modern metal alloys, care must be taken to insure that the tools are properly dissipating heat and structurally sound. Some metal alloys are not as susceptible to heat buildup which means that the tools will absorb more heat than normal, even when using a proper cutting oil.
Regardless of the heat issues, there still needs to be some oversight of the tool pieces and structural condition. With the varying degrees of flexibility in the metal alloys, there is also the potential for more resistance to cutting or spring back during the process. For more information see this: parlec.com